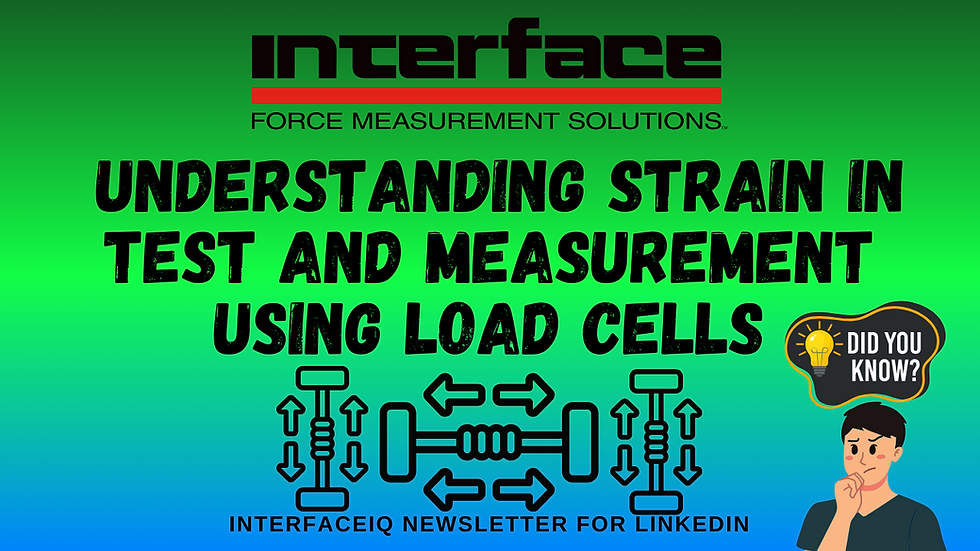
While often used interchangeably, engineers and material science know that stress and strain are fundamentally distinct. Understanding both is critical in test and measurement.
Stress represents the internal force per unit area within a material caused by an external force. It measures the intensity of the internal forces resisting deformation.
Strain quantifies the deformation or shape change of a material experience due to applied stress. It indicates how much the material stretches, compresses, or shears in response to the force. Strain is a unitless quantity regardless of the size of the unit length.
Strain is quantified as the ratio of change in length to the original length, expressed as a percentage or decimal.
Strain Testing: A Fundamental Tool in Material Analysis
Strain testing is a commonly used technique in test and measurement. It is practical and indispensable, offering valuable insights into how materials behave under different loading conditions.
Load cells are not just crucial in strain testing; they are fundamental. Interface load cells precisely convert changes in resistance into a voltage output, ensuring accurate measurements throughout the entire test, even up to the point of material failure.
By measuring strain under controlled loading conditions, engineers can determine:
Yield strength: This is the point at which the material permanently deforms.
Ultimate tensile strength: The maximum stress a material can withstand before breaking.
Elastic limit: This is the stress level beyond which the material will not return to its original shape after unloading.
Fatigue resistance refers to how well the material can handle repeated loading and unloading cycles.

Material testing is a standard strain test used in various industries. In this use case, a customer wants to conduct a tensile force test on different samples and materials until failure. Materials include plastic, steel, or woven fabric. Interface’s 1200 Standard Precision LowProfile™ Load Cell is installed into the customer’s test frame. The tensile test is conducted, and force results captured by the load cell and extensometer are synced through the SI-USB4 4-Channel USB Interface Module. The supplied software can display these results on the customer’s PC. Read more here.
Interface, a leading provider of force measurement solutions, offers a wide range of load cells ideal for strain testing applications. These sensors deliver high accuracy and reliability, ensuring precise strain measurements across diverse testing scenarios.
Five Reasons Why Strain Testing Matters
Material Selection and Design Optimization: By understanding how materials behave under stress, product designers and engineers can select the most suitable ones for specific applications. Strain testing helps ensure parts are neither overstressed nor underperforming, leading to optimal designs.
Strength and Durability Evaluation: Strain tests yield critical data on a material's yield strength (the point of permanent deformation), ultimate tensile strength (maximum stress before breaking), and elastic limit (stress level at which the material returns to its original shape after unloading).
Quality Control and Consistency: Strain testing is essential in manufacturing to verify that materials and products adhere to strength and performance standards. Manufacturers can identify inconsistencies and maintain product quality by testing samples from each batch.
Failure Analysis and Safety Improvement: Analyzing strain at the point of failure provides insights into the root cause, aiding in material selection, design enhancements, product development, and manufacturing process improvements to prevent future failures.
Cost Savings: Strain testing helps avoid costly product failures and rework by enabling informed material choices, design optimizations, and effective quality control.
Industry Use Cases of Strain Testing Using Load Cell Sensors
Construction: Evaluating the strength of concrete, steel beams, and other building materials to guarantee structural integrity.
Aerospace: Testing critical aircraft components like wings and fuselage to withstand extreme forces during flight.
Automotive: Assessing the durability of car parts like frames, axles, and suspension systems under stress.
Medical Devices: Ensuring the strength and flexibility of implants, stents, and other medical equipment used within the human body.
Consumer Goods: Verifying the robustness of everyday products like furniture, sporting equipment, and electronic devices.
Strain testing provides critical data for material selection, design optimization, quality control, failure analysis, and cost savings. Understanding how materials deform helps to create safer, more durable, and higher-performing products across various industries.
Comments